Unlocking the Potential of Digital Twins in Supply Chains
As companies optimize a wide range of supply chain functions with digital twins, the technology’s immense potential is gaining further recognition.
News
- Ooredoo Launches Sovereign AI Cloud in Qatar Powered by Nvidia GPUs
- Dubai Future Foundation and WEF Release Top 10 Emerging Technologies of 2025
- Deloitte and AWS Forge $1 Billion Alliance to Accelerate Digital Transformation in the Middle East
- Over 40% of Agentic AI Projects Expected to Fail by 2027, Report Finds
- Guardian AI Agents Poised to Take 15% of Agentic AI Market by 2030, Gartner Says
- Deloitte Rolls Out Global Agentic Network to Accelerate AI Adoption in the Middle East
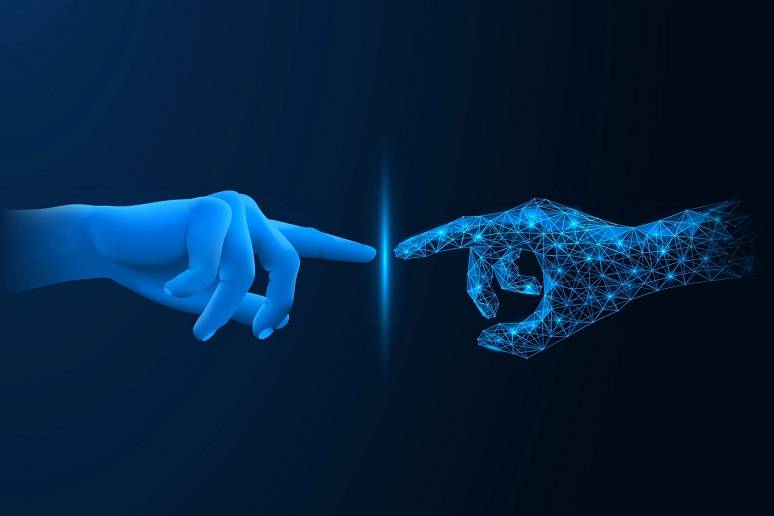
Since the early 2000s, digital twin technology has been adopted across many industries and become more accessible and affordable, yet it remains underutilized in supply chain management. This is partly explained by the complex nature of supply chains themselves and partly due to misunderstandings about the technology’s applications, capabilities, and potential value. However, with a proper adoption and implementation strategy, digital twins can deliver immense benefits across a wide range of supply chains.
Distinguishing Characteristics of Digital Twins
Digital twins — virtual replicas of physical entities and their interactions — consist of a combination of enabling technologies and analytics capabilities. But the technology is often misunderstood; many people incorrectly assume that digital twins are themselves sensors, 3D models, simulators, or applications of AI technology. Others mistakenly consider digital twins to be largely theoretical and not relevant for supply chain management, or assume that a digital twin can be built only after the physical twin has been created — but neither statement is true.
Digital twins are a combination of multiple enabling technologies, such as sensors, cloud computing, AI and advanced analytics, simulation, visualization, and augmented and virtual reality. Companies can use a customized mix of technologies, depending on their needs and expectations. What distinguishes digital twins and makes them so powerful is their ability to emulate human capabilities, support critical decision-making, and even make decisions on behalf of humans.
Digital twins observe their physical environment through a network of sensors that dynamically gather real-time data; they evolve by learning from this information and its contexts and by interacting with humans, devices, and other networked digital twins. Such a capability makes digital twins active and social tools, because they can continuously communicate and collaborate with their associated physical and digital objects and with humans. Digital twins support end-to-end visibility and traceability, enabling supply chain practitioners to spot patterns of highly complex and dynamic behavior.
Digital twins can oversee many internal and external moving parts in end-to-end supply chains and build nonlinear supply chain models. More critically, with their ability to compute thousands of what-if scenarios, the technology learns from these decisions and gains in maturity over time. This helps managers make faster, more accurate, and better-informed decisions with long-term impact at a considerably lower cost.
Supply Chain Applications
Our research at the MIT Digital Supply Chain Transformation lab shows that digital twins can improve business outcomes by discovering the complexities and behavior of the supply chain ecosystem and dynamically adapting, thus ultimately enhancing asset performance.
Supply chains have evolved to encompass much more than the linear movement of goods. Today, they comprise multiple layers of globally interconnected trading partners. Digital twins enable companies to mirror and map these complex systems and their underlying uncertainties, inform decisions, and adapt to an ever-changing operational environment.
In practice, a digital supply chain replica provides an end-to-end representation of the complex, real-world system that connects its component entities from suppliers, warehouses, and distribution centers to products and customers. By embedding AI in simulation scenarios, digital twins can help companies improve the efficiency of their supply chains across a broad swath of functional areas and analyze trade-offs between costs, service levels, and emissions. Specific examples of such applications include consolidating shipments in distribution centers, optimizing freight transportation fleets, testing warehouse layouts, adjusting goods flows and routing to align with demand, and supporting predictive maintenance programs.
At Amazon, digital twins dynamically optimize operations in the online giant’s physical distribution network. The company tracks shipments and streamlines product flows in real time to achieve high service levels in its two-day doorstep delivery services. Digital twins have helped pharmaceutical company GlaxoSmithKline develop a robust vaccine manufacturing process and better temperature-controlled product packaging through improved testing procedures. Similarly, home furnishings company Ikea uses the technology to predict the performance of new materials in sustainable packaging designs.
Leading companies have harnessed digital twin technology in three main functional areas:
Supply chain planning. Embedded into integrated business planning platforms, digital twins can enhance supply chain planning, from operational and tactical planning to strategic decision-making. Digital twins leverage multiple data sources to boost visibility and connect the dots between trading partners, in addition to leveraging static data stored in enterprise resource planning platforms. For example, by streaming real-time data from sensors and human interactions, as well as operational, financial, and commercial data, food and beverage company Kraft Heinz dynamically monitors inventory changes in warehouses, manages the location of items in real time, and predicts customer and channel demand more accurately to improve stakeholder experiences.
However, the primary value of digital twins in supply chain planning is in long-term decision-making. Philip Morris International (PMI) uses digital twins to simulate thousands of what-if scenarios that reflect the long-term outcomes of making strategic decisions. With this prescriptive analytics capability, PMI can analyze scenarios to better assess risks and prepare mitigation plans for potential disruptions. PMI also uses the technology to balance demand and supply, optimize trade-offs between resilience and efficiency, and analyze the ROI of costly investments over multiple time horizons. FedEx, too, uses digital twins to optimize its transportation fleet, asset utilization, and resource allocation, as well as to strengthen its ability to accurately forecast, identify, and minimize disruption and damage.
Warehouse management. Integrated into warehouse automation systems, digital twins can be deployed in a range of applications, from inventory management to facility design. Companies are now seeking digital twin solutions to simulate their warehouses and help them virtually test different floor plans in order to achieve optimal facility design. For example, the cold-chain warehousing and logistics company Lineage Logistics uses digital twins to optimize the design process before making any costly investments to construct physical warehouses. Simulating numerous what-if scenarios, digital twins consider factors such as facility location, customer profile, and demand characteristics to help the company determine uniquely fitting designs for each warehouse. Similarly, online grocery retailer Ocado Group deploys digital twins to mimic its existing grocery fulfillment centers in real time, simulating the outcomes of potential layout changes through its virtual replicas. This helps Ocado make accurate and cost-effective decisions without disrupting facility operations in the real world.
Although digital twins can yield significant business value in the design of warehouses and distribution centers, the impact of the technology becomes more significant in the long term when combined with inventory operations. Tetra Pak, a $13 billion packaging company, has pioneered the adoption of digital twin technology in warehouse management. A digital version of a company warehouse in Southeast Asia is fed operational data from the physical facility’s internet of things sensing infrastructure. The digital twin supports Tetra Pak in the management of stock locations, inventory, and workflows and in allocating warehouse equipment. As a result, the company achieves improved storage space utilization, increased operational efficiency, and enhanced workplace safety standards. Schneider Electric uses digital twins to automate warehouse operations and simulate the workings of the facility, processes, products, and personnel. With the help of the technology, the company monitors material flow, pallet movements at loading docks, and inventory positions, optimizing process design and resource allocation as well as offering operational and strategic insights to inform real-time decision-making.
Transportation management and last-mile delivery. UPS deploys hundreds of sensors in its trucks, hubs, and packages and collects inputs from drivers, employees, and customers to continuously gather the operational data generated by every entity in its extensive logistics network. These data points feed the company’s advanced analytics programs, helping to optimize UPS’s logistics network for increased efficiency and flexibility. Digital twins support this effort by tracking packages moving through the system in real time, from shipping label creation to final delivery. Digital twins can also learn individual customers’ behavior — such as delivery and packaging preferences, number of orders shipped and received, and interactions with delivery drivers — and analyze drivers’ on-road behavior and safety compliance. In addition, the network’s virtual replica performs dynamic route optimization and navigation tasks, and manages dynamic capacity allocation and package dispatching routes in hubs.
The Way Forward
While the above examples prove the value of digital twins in supply chains, they represent only a fraction of the technology’s potential applications. More companies can take advantage of the technology if they approach its adoption and implementation in a systematic fashion.
Before investing in digital twin technology, enterprises must assess and analyze their current supply chain functionality. Which supply chain actors are involved? Which KPIs need improvement? Which data sources and analytics capabilities are currently available? It’s essential to answer these questions in order to identify exactly which supply chain outcomes to improve — and, more practically, to pinpoint which core functions the digital twin will mimic.
Companies can start by building a digital twin for the most relevant and pressing supply chain function and scale up to connect with digital twins for complementary functions. This connection creates a digital twin network that, over time, will help the company improve the efficiency of its end-to-end supply chain.
As implementation costs continue to decrease, the time between initial efforts and investments in digital twin technology and the break-even point will decrease as well. Digital twin enabler technologies are paving the way for faster adoption across functional areas, positioning digital twins to play an increasingly important role in supply chain digitization as companies advance in using the technology to improve functionality and orchestrate their digital transformation journeys ever further.